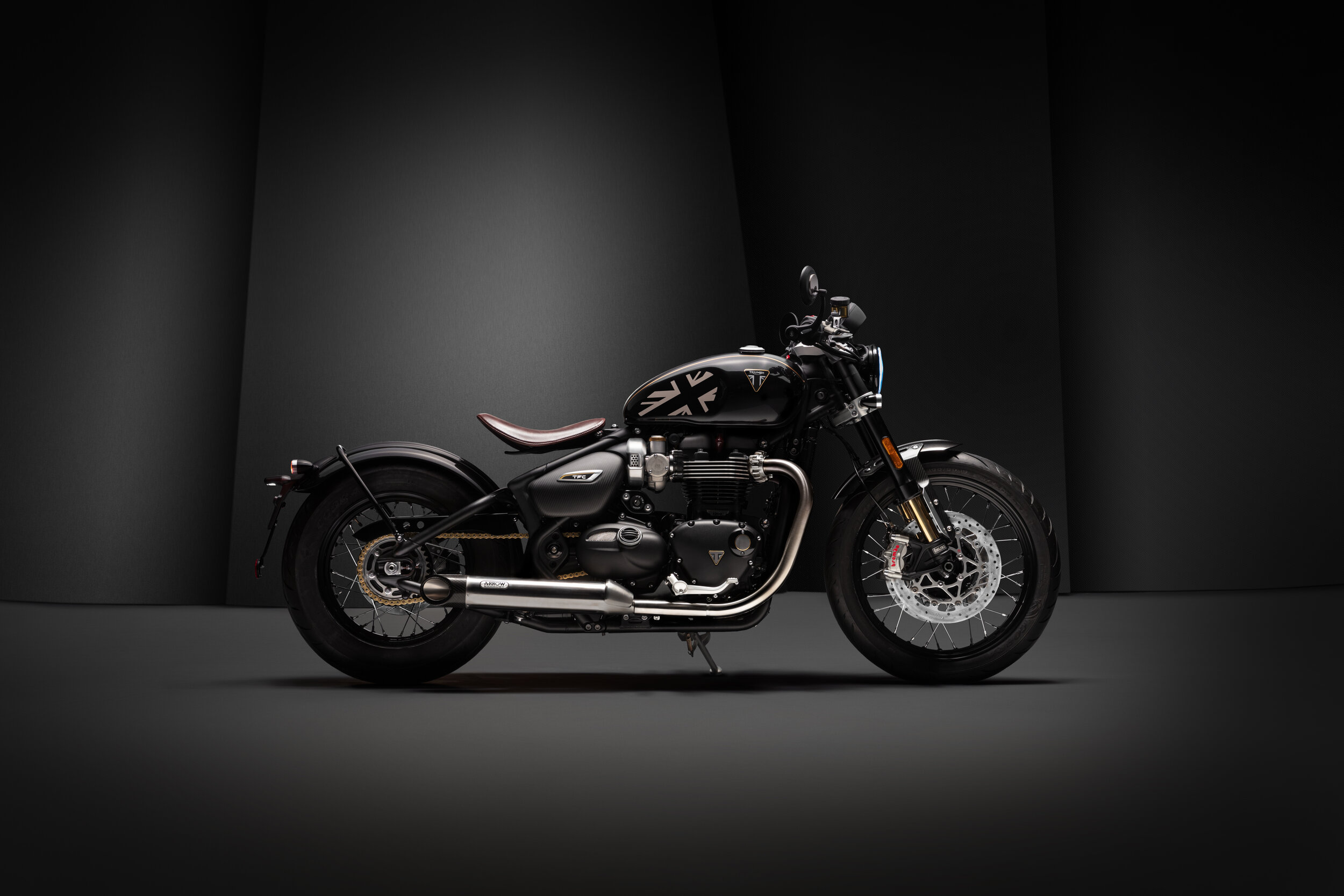
Design Services
Dovetailing and overlapping
The final product is our absolute focus.
Our design services and processes are a means to that end and everything we do is in the service of that goal
2019 Triumph Rocket 3
Services
The final product is always our absolute focus; our services and processes are simply a means to support that end and everything we do is in the service of that goal.
CHD Design Works has the full range of services in-house to deliver a project from concept initiation to production release.
Optimisation and efficiency of the design process is important to us. The design phase of a project is finite, and deadlines are there to be met not missed. By bringing in-house all the key elements that are required to deliver a motorcycle or powered two-wheeler project we are able to maximise the value-added design time. We are well-used to dovetailing and overlapping the various stages in such a way as to reduce non-productive lead-times to an absolute minimum.
Our purpose-built design studio, which we moved into in 2018, forms an integral part of this overall capability.
Design Process
Clearly different clients will manage their projects in different ways and CHD are able to adapt to the specific requirements of each case.
We have also experienced and developed a range of different approaches over a number of years and are able to recommend an appropriate route to production for clients who may be wanting to improve their processes or are looking to CHD to take a fuller overview of the delivery of the wider project.
For the purposes of describing our work here we have divided the phases as follows:
Concept Design (and Pre-Concept)
Design Development
Design Release
Final Sign-Off
Production Release

Concept Design

Design Development

Design Release

Final Sign-Off
Concept Design Phase
Concept ideation (sometimes ‘pre-concept’) is a key part of our work at CHD. We are able to deliver to a variety of customer requirements from wide-ranging design investigations to focussed specific proposals working to very tight constraints. Outputs cover the full spectrum from sketch reviews to fully rendered 2D proposals for customer clinics to 360 degree rendered 3D CAD presentations.
Our usual definition of the concept stage would end with the release of 3D CAD surfaces that have been worked through to varying degrees of feasibility (as required) with the concept engineers in our clients’ organisations or have been through the concept engineering phase within CHD. The designers and engineers in our team are fully conversant with the manufacturing processes required in the manufacture of a powered-two-wheeler and by the end of the concept phase due regard will, by default, have been paid to manufacturing methods and constraints, materials and finishes, homologation requirements and BOM implications. The level of detail at this stage will depend on the client’s requirements.
The concept phase also quite often includes a concept clay model followed by further CAD refinement or at other times may just require the 3D CAD release. Scale models are also sometimes used to good effect at this stage to investigate design options but generally where physical clay development is a key requirement at the concept stage, a full-size model would be more usual.
CHD’s team are all conversant with 3D CAD and this is our default method of communication once the sketch ideation phase has been passed.
Between our Designers, CAD modellers, A-CLass Surfacers and Concept Engineers we use a variety of software packages to suit the full range of work from concept initiation through to final A-Surface release.
The software packages in daily use at CHD include:
PTC Creo, Autodesk Alias, Siemens NX, Polyworks, Rhino 3D, Autodesk VRED and Work NC.
Design Development Phase
Design Development post-Concept for us usually takes the form of a full-size clay model. If this is the case, then we have full capability to design and build our own styling bucks and to manufacture the necessary components in-house or by out-sourcing, or by a combination of both, depending on the particular design of the buck and/or our capacity at the time.
We have a full-sized 3-Axis clay mill at CHD, capable of machining an entire fully-faired motorcycle in one set-up if required, in either model-board or clay. We generally machine the clay armatures and clay surfaces ourselves in-house as this allows us to manage the development of the data up to the very last moment before machining, thereby removing the ‘design freeze’ stage which would otherwise be required. Where multiple projects might stretch our capacity, we have very reliable and flexible suppliers on our doorstep who are also able to meet the particular requirements of last-minute data release to eliminate design down-time.
Output at this stage can be raw clay, painted clay, or anything in between, depending on our clients’ requirements. These models will usually be a combination of hand-worked clay, hand-made hard models and CAD-built SLAs, SLSs and similar.
We also have wide experience of delivery ‘straight to CAD’ and for the right product and the right client this can be a highly effective way forward.
Throughout the design development phase, we would usually be releasing CAD, either scan or surfaces, to our clients as required and iterating between clay and CAD as necessary. At the same time, sketch development and initial CAD development of detailed components would continue in parallel, gradually filling out the detail design intent and feasibility, either in partnership with our clients’ engineering teams or in-house at CHD.
Design Release Phase
The later stages of a project usually require A-Class CAD surfaces to be delivered either by CHD or by our clients’ in-house surfacing teams or, more often than not, by a combination of both.
In parallel with the development of the ‘reverse-engineered’ clay surfaces, we would also be engaged in final CAD surface release for all other detail components, for chassis, engine (or increasingly, electric motor) and drivetrain.
Final sign-off
Final sign-off is generally by the presentation of a full-size hard model (a painted model simulating a production motorcycle). CHD are fully capable of creating and finishing entire full-sized painted models using a variety of processes, some of which are out-sourced and some in-house. A gallery of some of our hard models can be found by clicking through the hard model image on this page.
CHD also have experience of fully digital methods for final sign-off and approval presentations. This would usually be in the form of a fully rendered VRED presentation including raytracing.
Click below to see a gallery of some of the hard models CHD have made over the years
Production Release
CHD expect to retain responsibility for styling up to the start of production, and if necessary beyond.
The time at which the design integrity of a project is most at risk is in the post sign-off delivery stage where changes come pre-loaded with serious consequences to design intent, production and project costs and project timings.
CHD are fully conversant with the constraints and urgency that can dominate design decisions at this stage and have a strong record of finding appropriate and practical solutions within near-zero timescales, whilst maintaining the integrity of the final output.
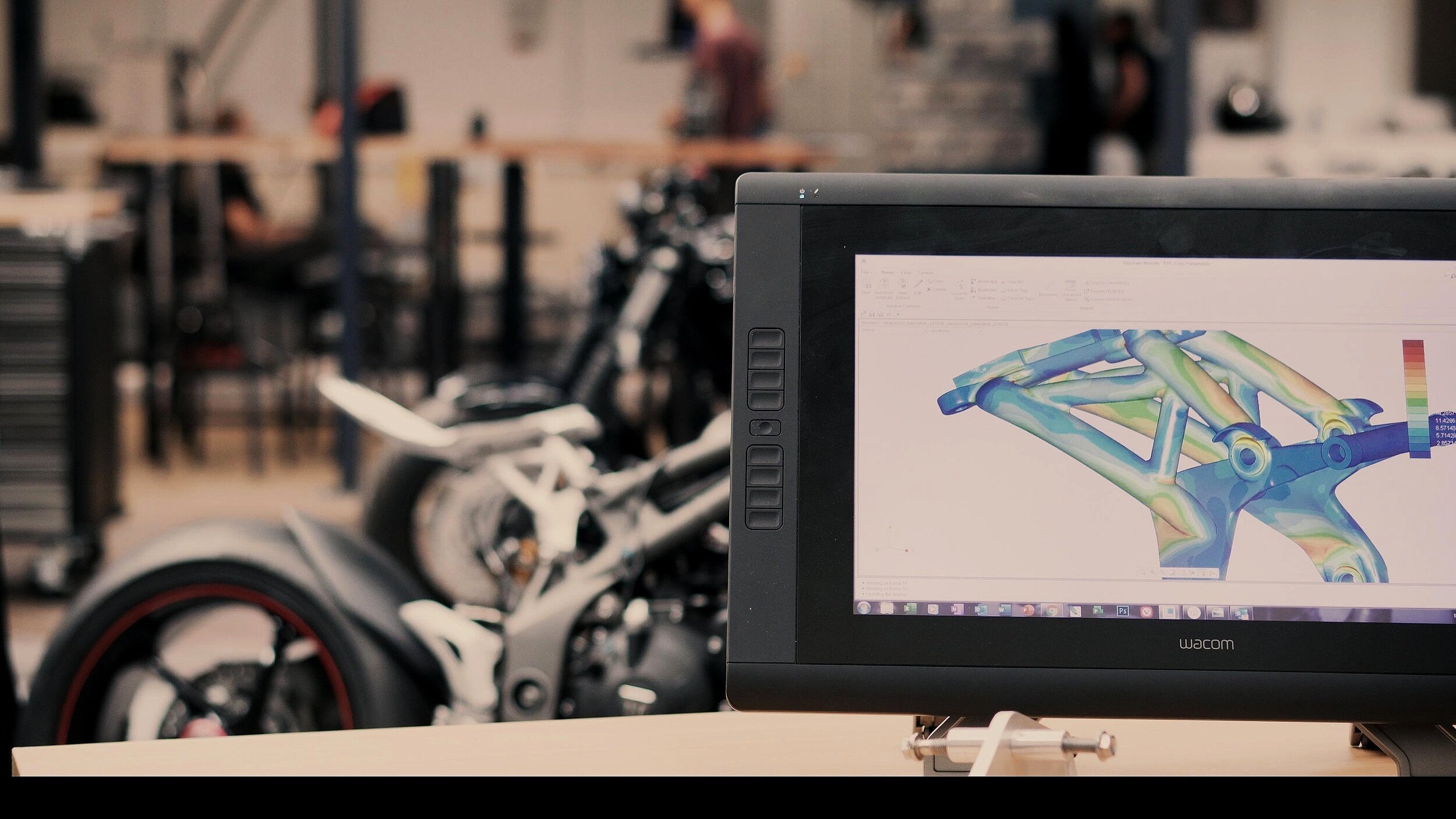